Staying on the Cutting Edge: Your Woodworking System FAQs Answered!
May 01, 2024
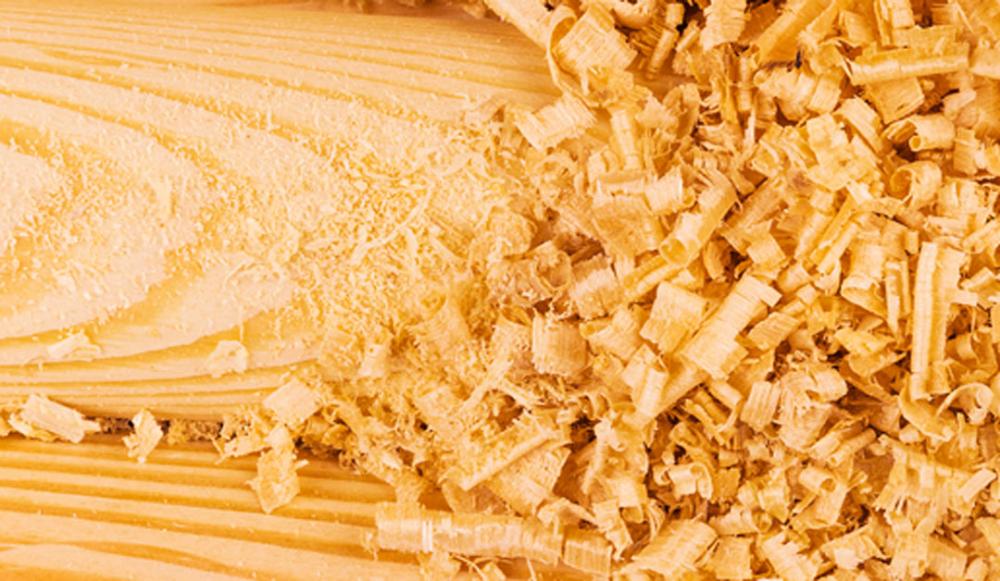
An Overview of Vacuum and Blower Systems for Woodworking and Carpentry
Woodworking is a complex and demanding industry requiring efficient and reliable equipment. When it comes to vacuum systems, regenerative blowers and dry rotary claw pumps are two of the most popular options. In this article, we will address the questions we hear most frequently.Q: What is a vacuum pump used for in woodworking?
A: A vacuum pump is a versatile tool used in woodworking for various tasks, including veneering, clamping irregularly shaped or curved pieces of wood, dust collection, and CNC routing. One of the primary uses of a vacuum pump in woodworking is for veneering. Veneering is the process of applying a thin layer of wood, called veneer, to a base material to create a decorative finish. A vacuum pump is used to create suction, which presses the veneer against the base material, ensuring a tight, even bond. Another common use of a vacuum pump in woodworking is for clamping. A vacuum clamp works by creating a negative pressure that holds the workpiece in place for sanding, routing, carving, gluing, and more. Vacuum clamps are particularly useful for irregularly shaped or curved pieces of wood, where traditional clamps may not be effective. Vacuum systems are also frequently used as a hold down apparatus for CNC tables. Finally, a vacuum pump can also be used for dust collection in a woodworking shop. As woodworkers cut and shape wood, they generate a significant amount of sawdust and other debris, which can be hazardous to breathe in. A central vacuum pump system can be both to clean dust from surfaces and to collect dust from the air. This helps to keep the workspace and environment clean and free from harmful dust particles, improving the overall safety of the shop.Q: What is the difference between vacuum clamping and mechanical clamping?
A: When it comes to clamping for woodworking, both vacuum clamping and mechanical clamping have their own advantages and disadvantages. Vacuum clamping may be more accurate, efficient, and damage-free, but mechanical clamping can provide a stronger hold and is more versatile. The choice of clamping method ultimately depends on the specific project and personal preferences of the woodworker. Let's take a closer look at the benefits of each method.Vacuum Clamping:
Vacuum clamping is a method of securing workpieces by creating a vacuum between the workpiece and the work surface. It involves using a vacuum pump to suck the air out of a sealed chamber, which creates a negative pressure that holds the workpiece in place. Here are some of the benefits of vacuum clamping:- Increased accuracy: Vacuum clamping allows for precise positioning and holding of workpieces, which can be especially useful when working with small or delicate pieces.
- No marks or damage: Because vacuum clamping uses suction rather than pressure, it won't leave marks or damage on the workpiece or table. This is especially important when working with delicate or expensive materials.
- Increased efficiency: Vacuum clamping is often faster than mechanical clamping, as it doesn't require the use of clamps or other hardware. This can save time and increase productivity.
- Greater accessibility: Vacuum clamping can hold down oddly-shaped or non-uniform workpieces that may be difficult to secure with traditional clamps.
Mechanical Clamping:
Mechanical clamping involves using clamps, screws, or other hardware to secure workpieces to a table or other surface. This method has been used for centuries and is still widely used today. Here are some of the benefits of mechanical clamping:- Stronger hold: Mechanical clamps can provide a stronger hold than vacuum clamping, as they use pressure to hold the workpiece in place.
- More versatile: Mechanical clamping can be used to secure a wider range of workpiece sizes and shapes, as there are a variety of clamps and hardware available.
- No need for additional equipment: Unlike vacuum clamping, mechanical clamping doesn't require any additional equipment, such as a vacuum pump or hoses.
- More affordable: Mechanical clamping can be a more affordable option than vacuum clamping, especially for hobbyists or those who don't have a large budget.
Q: What is the fastest way to dry wood?
A: The fastest way to dry wood is through a process called vacuum drying. In this process, the wood is placed in an airtight chamber and the air is removed using a vacuum pump, creating a negative pressure. This causes the moisture inside the wood to evaporate more quickly, and the water vapor is removed from the chamber using a dehumidifier or condenser. The process can be faster and more efficient than traditional air drying or kiln drying methods and can help prevent warping or cracking of the wood. However, it does require specialized equipment and knowledge to ensure the wood is dried correctly and without damaging it. The most popular choices of vacuum pumps for vacuum drying and other woodworking applications are dry rotary vane pumps, rotary claw pumps, and regenerative blowers.Q: Do dry rotary vane pumps work well for woodworking applications?
A: Dry rotary vane vacuum pumps have long been the standard for woodworking applications and is considered the workhorse of the industry. However, rotary vane pumps are the technology of yore. Will they work? Yes, but relying on this mechanism might cause you to miss out on the benefits of more advanced technology. The essential design of a rotary vane pump naturally creates friction; as the vanes rotate to create vacuum, they scraping along the sides of the chamber. Rotary vane pumps—both dry and oil-lubricated—require more horsepower and a higher energy utilization to overcome this friction and generate the required vacuum. . In addition, the vanes naturally wear, requiring replacement every 3000 hours or at least once a year. If the vanes are not changed in time, they can break, causing catastrophic pump failure. Despite this, dry rotary vane vacuum pumps remain a popular and reliable technology with a low up-front cost. Republic Manufacturing offers a full range of dry vane vacuum pumps well-suited for the woodworking industry. They are easy to install and operate as a direct replacement for many of the other brands. Vanes, gaskets, filters, and other replacement parts are available at the ready. So, if dry rotary vane technology is your comfort zone, we’ve got you covered. If you are interested in other technologies listed above, we are happy to work up an estimated return on investment.Q: What are the benefits of using rotary claw or regenerative blower technology over rotary vane pumps? How much money can I save?
A: One of the main concerns of woodworking companies is energy efficiency and cost savings. Regenerative blowers and rotary claw pumps are designed to address these issues. Regenerative blowers with VFD (variable frequency drive) and pressure transducer technology can help reduce energy consumption significantly. By using a smaller motor and only running the RPM that is required for the pressure, regenerative blowers can save energy and reduce costs compared to traditional blowers. This technology allows the Regenerative Blower to use a smaller motor and run only the required RPM for the pressure, resulting in reduced energy consumption and cost savings. Regenerative blowers are maintenance-free – only a filter to change! Dry rotary claw pumps use smaller motors which consume less energy, resulting in lower energy consumption and cost savings. This technology is nearly maintenance-free – no vanes or oil to change! The only maintenance parts on a claw pump are roughly one-quarter of gear oil and an inlet filter. These technologies require less power than high-friction rotary vane pumps, saving money on energy costs. They also have minimal wearing and maintenance parts, further reducing maintenance and repair costs and making them an attractive option for companies looking to optimize their operations.\Q: What if I’m interested in switching to a new pump technology?
A: No problem! Get in touch with us, and we will address your needs to ensure you are using the best technology for your exact application. We will review the following:- Vacuum and flow requirements based on table size, material, elevation, and cut sizes.
- Power availability.
- Connection sizes.
- Workshop layout
- And more!